These are the most important parts of any Aerial-type reel. As any reel-maker will confirm, the spindle must be turned absolutely true and to size. The hub which runs on it must have a precision size & parallel bore, with the spoke holes correctly positioned both radially and longitudinally. Also, the grooves for the forks have to be in the right places, with particular regard to the very small slots at the bottom of the grooves, as the rearmost one positions the line drum on the spindle. It's not really as difficult as it sounds but with a very small margin for error on any of the dimensions, it's not the sort of job you can rush..if you want to get it right and not just 'near enough', which is not acceptable.
I've been working on this about one hour each evening this week and have managed to make good progress on these two components. There are still some tasks to complete but this is what we've done so far..
..Starting with the hub then; the first thing was to put a billet of material in the chuck and rough it down to size, plus a little for finishing. This piece of nickel-ali. bronze is of the highest quality and can run with only minimal lubrication, which is ideal. Most of these pictures are very similar to the Coxon Aerial project so I hope you don't mind.
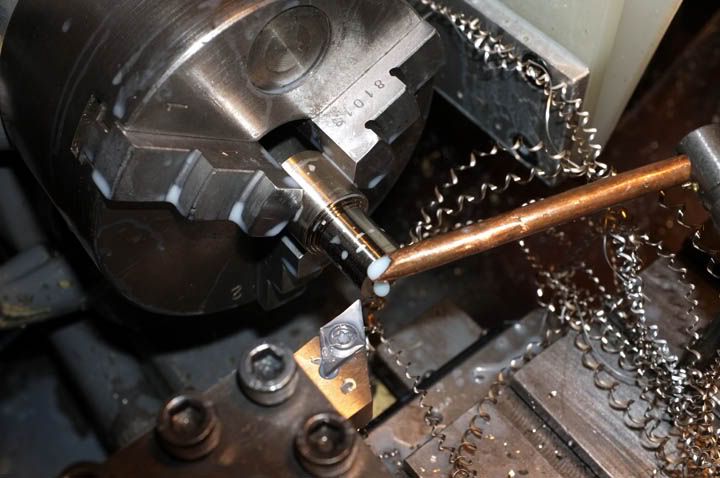
The next thing was to drill the hole for the spindle. This is 0.010" undersize to allow for finish-boring. It has to be bored because no drill can be expected to cut both dead to size, dead concentric and with good finish.
After that was done, the drilling attachment was set up and the six holes for the rearmost spokes were spot-drilled, 60 degrees apart. This is to ensure that the drill itself starts in the right position and does not 'wander'.
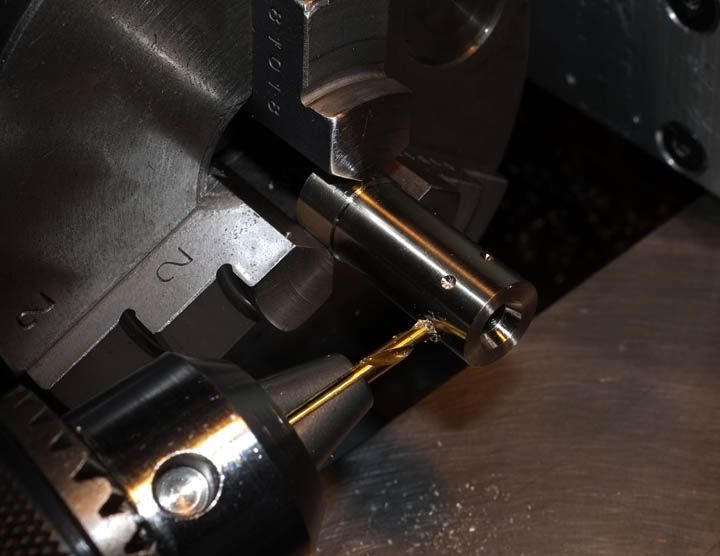
They were then drilled 1.25mm diameter through to the bore...
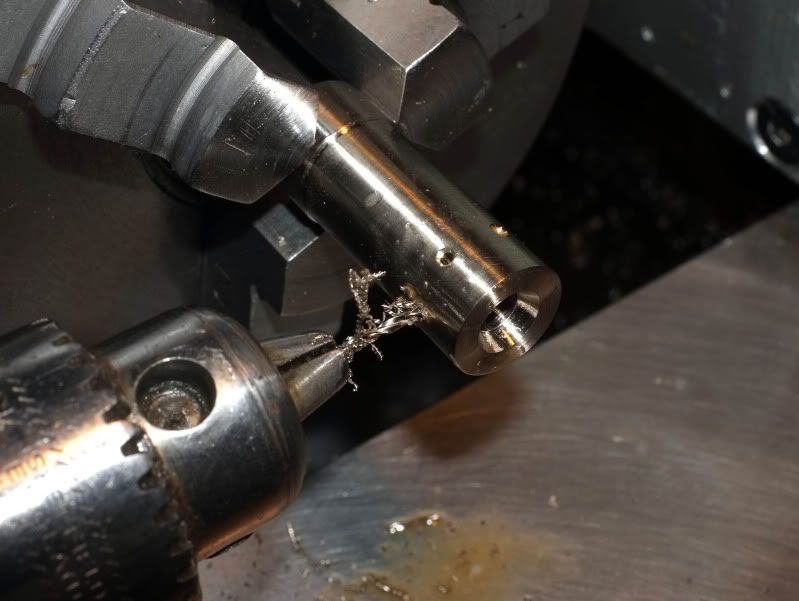
...and tapped with a M1.6 x 0.35 pitch tap. If you are having a go at this, the tap is very small and very brittle, so go easy..!
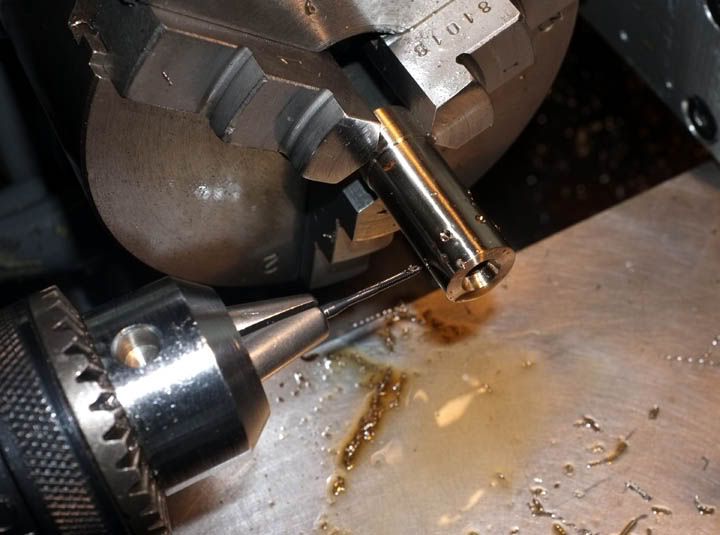
All six were completed without mishap so the attachment was indexed along to the right spacing for the outermost spokes and then indexed radially 30 degrees before drilling & tapping the second set of six in the same fashion.
The next job was to bore out the drilled hole to the spindle size. It was necessary to do several 'spring' cuts to allow the tool to produce a perfectly parallel bore of good surface finish.
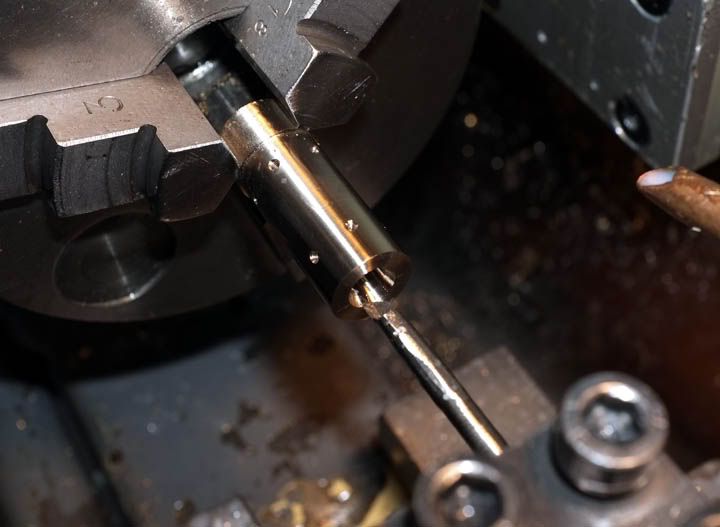
This was carefully checked for parallel and size, using a small internal micrometer.

This is a great little instrument-and the only one to really accurately measure a small bore. It is part of a set of three (complete with their own calibration gauges), which can measure up to 12mm diameter (0.47244") and have been worth their weight in gold when making new rod ferrules, where you must work to 0.0001" tolerance.
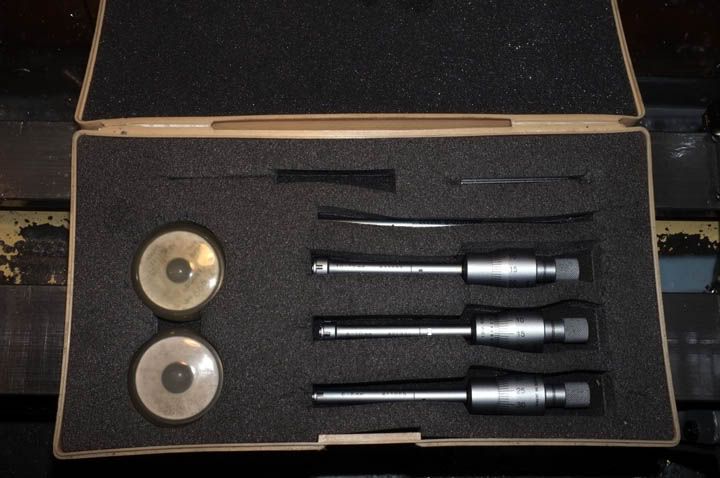
The next thing was to put in the fork grooves..
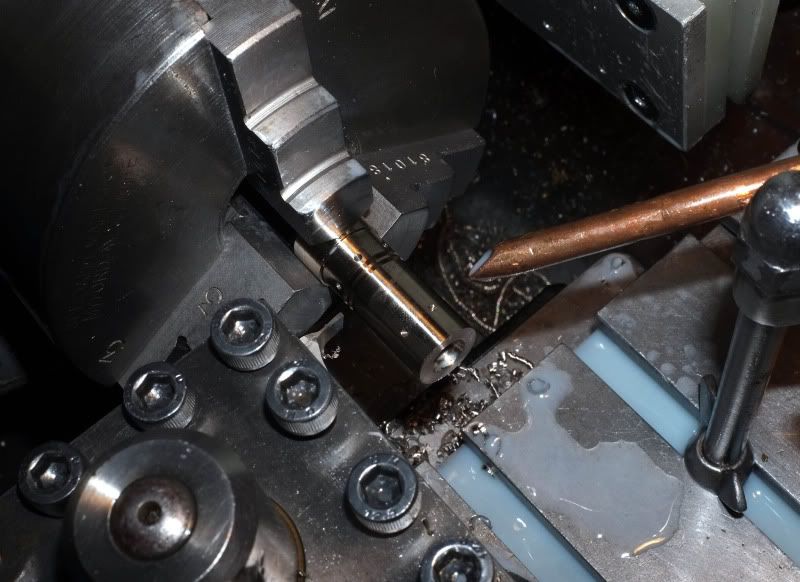
...and then turn the diameter for the check wheel. When that was done, the centre portion was relieved by turning down to 5/16" diameter.

The small step diameter was put in for the end cap and the hub was then 'parted of'.
The Spindle.
As before, this was made from 17/4 ph stainless steel; a most excellent material for the job and one which will not react chemically or physically with nickel ali. bronze.
All turning operations were done without removing the work from the chuck, thus guaranteeing concentricity. Here, most of the turning has been done and we are producing the backplate location diameter. This is vital, as the running clearance between line drum and backplate will be only 0.002" to avoid line-trapping.
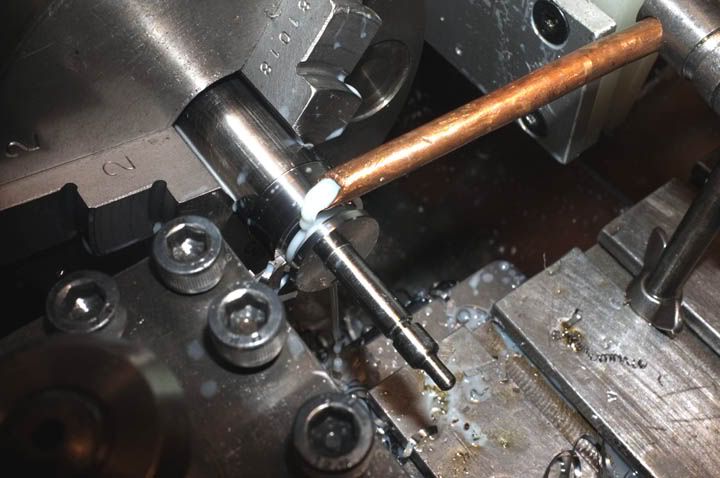
Finishing the location diameter. The front taper has yet to be done and it is then all polished to size..
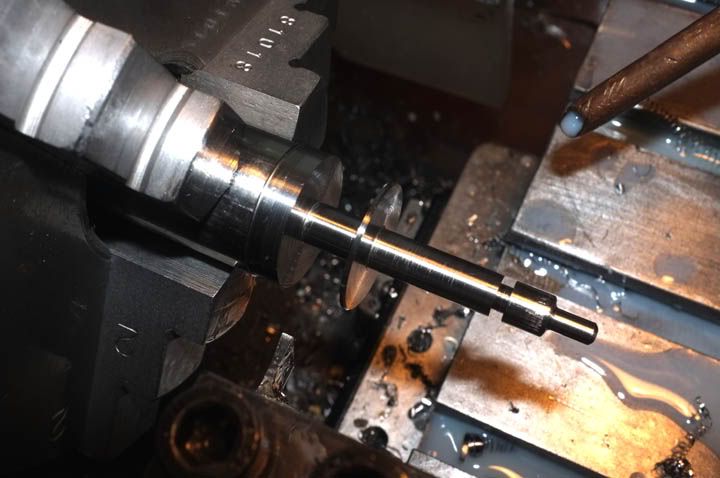
Checking the hub for fit..
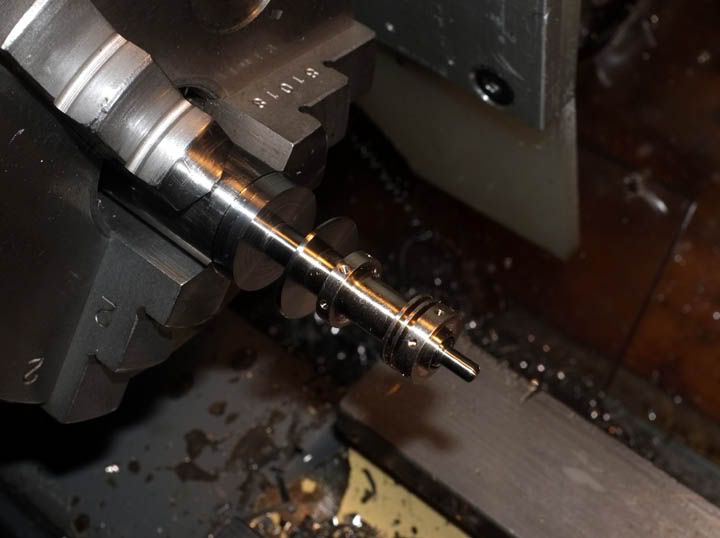
That completes most of the work on this part. Next time, we are going to make the star back and reel seat. Looking at it now, although it looks OK on that type of reel, it was rather unnecessarily OTT on metal thickness, so this time it's going to be a bit more in keeping with what is required..
Regards for now,
wm+